General aviation cockpits increasingly have electric pitch trim, both manual and autopilot-controlled, bringing a corresponding increase in incidents and accidents related to these systems. For manual electric trim, the trim servo-motor is activated by a switch on the control yoke. Manual electric trim aids flying as you needn’t break your visual concentration to reach for the trim wheel.
Newer, more sophisticated digital autopilots also have auto trim to complete the autopilot installation. Without the autopilot being able to trim the aircraft, the autopilot is only halfway flying the plane as you must manually adjust the trim. Configuration changes like dropping the gear and changing the flap settings are where auto trim shines.
Many failures can cause a trim issue, but we’ll limit the discussion to trim runaway, a failure that causes the trim servo motor to run continuously. If you don’t stop it, the trim will run to the stop, control forces will be high, and the aircraft will be difficult or impossible to control. Trim accidents can happen to any pilot, from beginning student pilots to experienced ATPs. However, without “electric trim” you won’t experience a runaway. The manual trim can fail, but normally that’s less hazardous than a trim runaway.
What Causes a Trim Runaway?
Anything that causes the trim servo motor to run continuously, without pilot action, will cause a trim runaway. This can be as minor as a stuck pilot trim switch, to an autopilot malfunction. The stuck switch will typically be obvious as the button didn’t return to center. An autopilot-induced trim runaway is less obvious and typically has delayed reaction time. Technically, you are the pilot flying (PF), but George, the autopilot, is flying and you are the pilot monitoring (PM). The PM who must determine the cause and take corrective action.
We’ll discuss two trim runaway incidents later. These involved professional crews who managed the situation; the cause of the trim runaway was later determined on the ground. Often, trim-runaway accidents destroy the aircraft leaving the exact cause unknowable.
This was the case of the crash of a Citation II into Lake Michigan on June 4, 2007. From the NTSB accident report, the pitch-trim jackscrew and cockpit indication were found full nose-down. A Cessna flight test in a similar airplane showed that full nose-down trim at 150 to 250 knots resulted in stick forces of 72 to 100 pounds.
The NTSB concluded that the accident sequence started with a control problem related to either an inadvertent autopilot activation or a pitch-trim anomaly, the effects of which were compounded by aileron and/or rudder trim inputs; however, it was not possible to determine the exact nature of the initiating event. The manual electric trim, auto trim or the artificial control feel system can cause a trim runaway. Let’s look at those possibilities.
Manual Electric Trim
As reader Jerry LeCroy commented about the Autopilot Trim article (IFR Magazine August 2023) the S-TEC wiring for the manual electric trim provides an efficient way of reversing the current to the trim servo motor, thus changing the trim direction. Also, the installation can be fault tolerant, where a single failure will not cause a trim runaway. To be fault tolerant, it must have two independent momentary switches on a split switch assembly, as shown in the photo above.
If you look closely, you can see there are two red switches, not one. Using a single switch will work, but it would be subject to internal failures. A typical switch spec sheet shows between 10,000 and 50,000 operations before the switch fails, but you need to consider how many times it is operated on each flight. On the other hand, not every switch failure will cause a runaway. Additionally, if both the left and right yokes have trim switches, the probability of a trim switch failure doubles. Plus, chafed trim wiring in the control yoke was found in three of the accidents/incidents we’ll review.
Certification requirements in 14 CFR Part 23 state that no more than 60 pounds of force may be required to overcome an electric pitch trim that has run for three seconds. This is significant, but incomplete. While not stated explicitly, if the trim is not stopped within three seconds, the stick force can continue to increase by 20 pounds per second as it continues to run. For example, if the trim has run for five seconds, an override force of 100 pounds will meet the certification requirements. Thus, a trim runaway to the stop is a dire emergency.
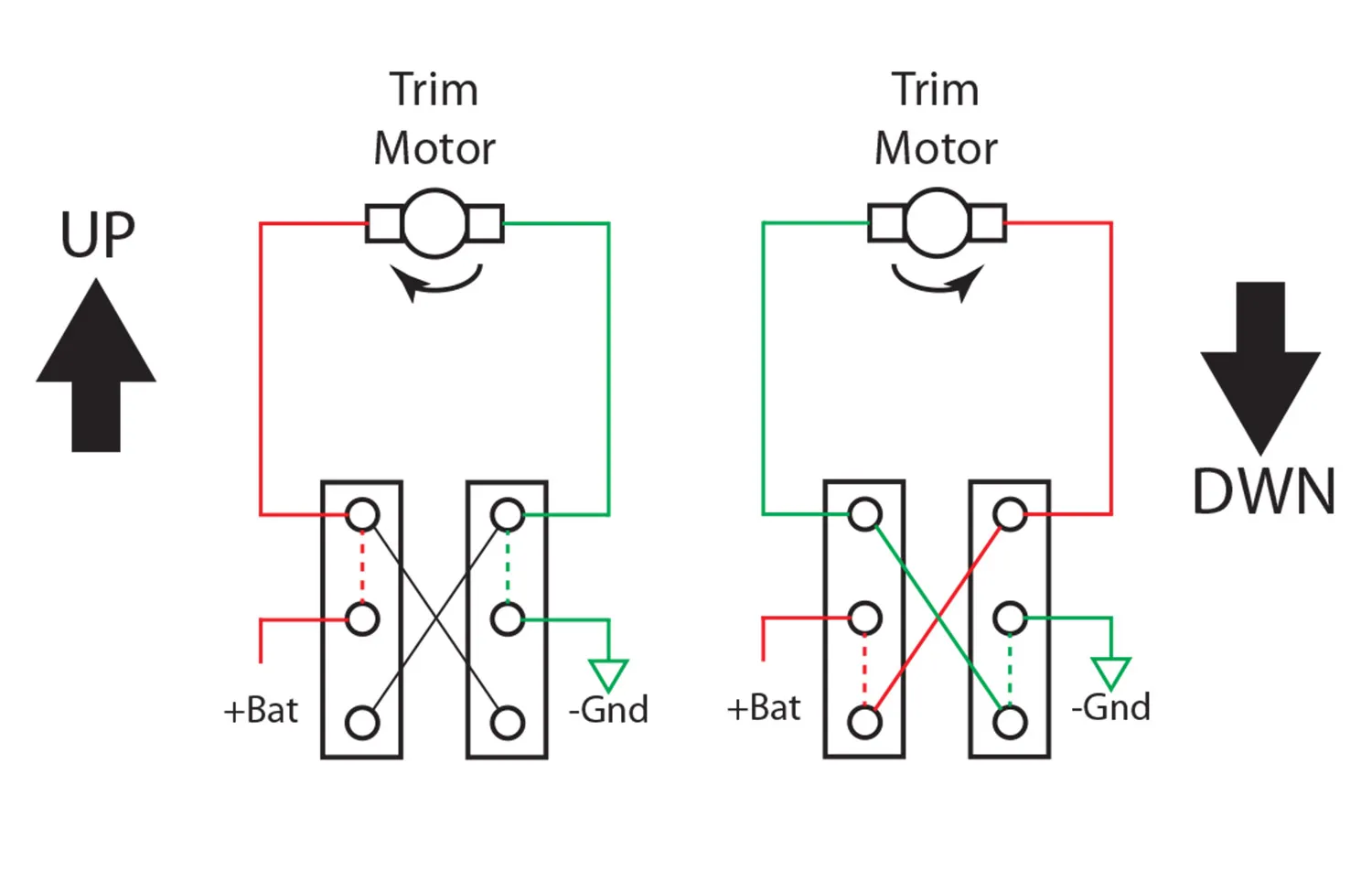
Autopilot Trim
The autopilot trim serves the same function as manual trim—it relieves the force held by the autopilot servo and will generally use the same motor as the manual electric trim. If it’s the same motor, activation of the manual electric trim should disconnect the autopilot. In normal situations, for a configuration change the autopilot commands the pitch servo to pull on the elevator cable. If the force is constant for a few seconds, the trim servo will activate to reduce the force to near zero.
The FAA certification requirements specify a three-second time for the pilot to recognize an autopilot problem and take action. Therefore, the designers usually provide at least a three-second delay before the trim starts, so you don’t have to fight the autopilot and trim servo in case of a failure. This is reduced to one second on approach.
As noted, the stick force can increase 20 pounds a second. Except for an engine failure shortly after takeoff where immediate reflex action to lower the nose is required, being slow and deliberate is the best policy to handle most aircraft emergencies. But every second counts in a trim runaway. Be deliberate but fast—as Wyatt Earp said about gunfights: “Be slow in a hurry.”
The FAA allows systems that are “fault-tolerant,” “fail-safe,” or have automatic detection of runaway conditions to operate the trim faster than those without. A fail safe system requires multiple failures before something hazardous happens.
Digital autopilots facilitate fault-tolerant designs with faster trim speeds. Plus, most modern auto-trim systems vary the trim speed inversely with airspeed—slower trim speed at cruise than on climb out or approach. Increasing the trim speed is good for aircraft control, but gives less time to recognize and overcome a runaway.
Auto trim brings additional failure modes. The monitoring circuit that measures the amount of servo force being held can fail, telling the autopilot to command trim when it is not required. A short-circuit internal to the autopilot computer or the associated aircraft wiring can also lead to a trim runaway.
Artificial-Feel Systems
A natural extension of auto trim is artificial-feel systems. Early systems modified stick forces using springs for improved control feel. Spring tension could vary with the dynamic air pressure or it could just add a constant nose-down force. Other systems used bob weights. However, with digital systems it is more economical and precise to utilize the autopilot, particularly the pitch and roll trim servos for improved control feel or to alert the pilot that they are exceeding normal pitch or roll attitudes. Without pilot action this system increases stick forces when the roll or pitch exceeds certain limits. These systems are widely regarded as a substantial safety improvement for the GA community.
While not a classic case of trim runaway, the Boeing 737 Max illustrates what can go wrong with artificial-feel systems with automatic pitch trim changes. The MCAS was designed to give the B-737 Max flight crews the same feel as the earlier model 737s. MCAS used stabilizer trim to stiffen the feel through the yoke. Unfortunately, under certain circumstances, it could eventually command full nose down trim.
Two Trim Runaway Incidents
The first incident was a failure in the force monitoring circuit that causes the autopilot to command trim. The aircraft, a Dassault Falcon 7X, experienced a nose-up trim runaway. Still, the flight crew quickly recognized the problem and used excellent airmanship skills to prevent this incident from becoming fatal.
Descending to the destination, at approximately 13,000 feet, the trim went from level to full nose-up in 15 seconds. The pilot flying (PF) made full nose-down inputs. When that proved ineffective, he banked the airplane right, initially to 98 degrees as he had done during his military career as a fighter pilot in the French Air Force. This maneuver changed the nose-up pitch into a bank, [from the report] enabling the pilot to temporarily regain pitch control despite the trim being in full nose-up position. At that point, triggering a change in the trim control channel, the pilot could once again control attitude via the sidestick. Two minutes and 36 seconds elapsed until the return to level position.
What caused the trim runaway? Micro-cracks on the induction coil solder (bad solder joint) caused the runaway. The bad solder joint caused feedback to the autopilot to be incorrect and the autopilot kept applying more nose-up trim. Findings dealt with details of the soldering process and the solder itself. The full BEA (French NTSB) report can be found online by searching BEA HB-JFN 24 May 2011.
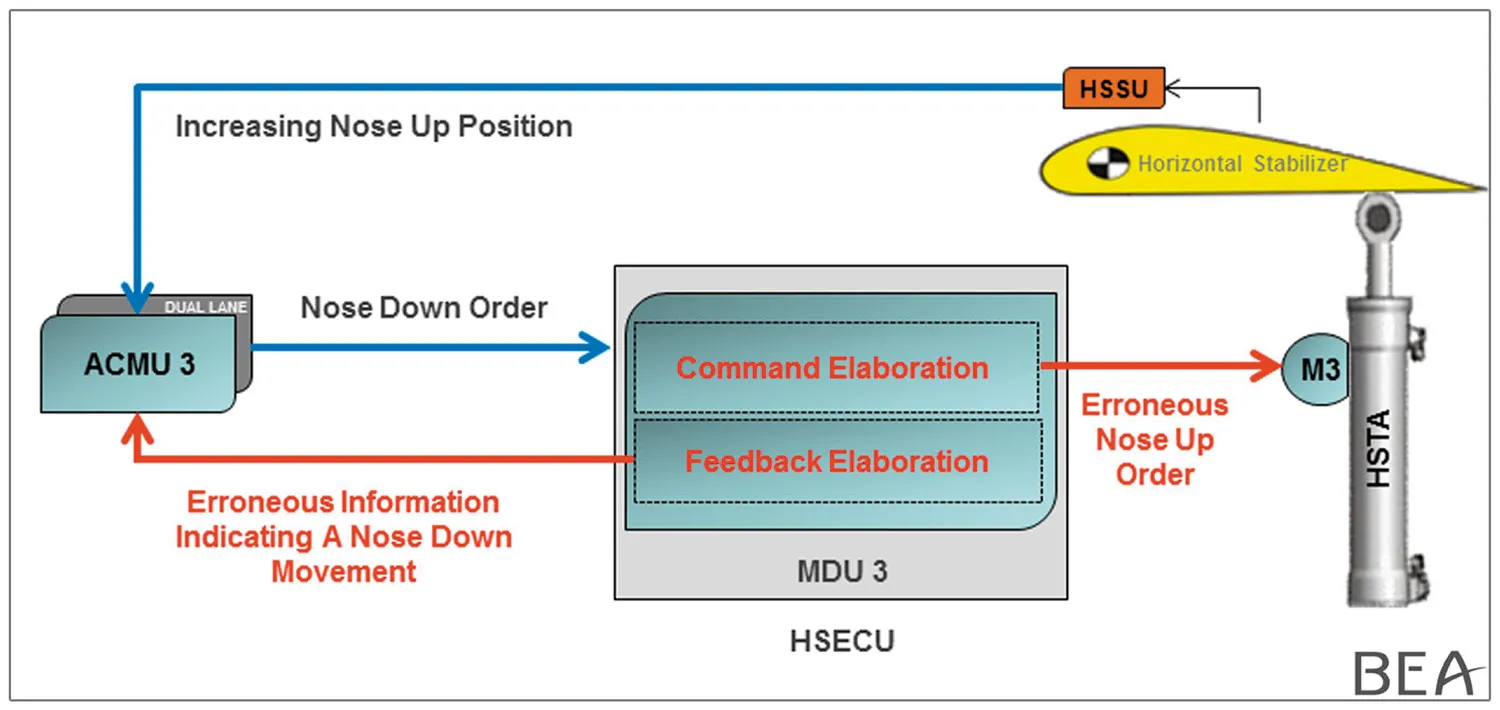
The second incident was an Embraer 175 flight on November 6, 2019. Its routing took the aircraft on three legs from DTW to LGA, to ATL, and back to LGA. During the first leg from DTW to LGA, a message annunciated Pitch Trim SW 1 Fail. The captain further stated they referenced the quick reference handbook and since the EICAS message was advisory only, they wrote it up in the aircraft logbook to be addressed at LGA.
At LGA, maintenance advised the crew that they would change the captain’s pitch trim switch to resolve the message, but it would take 20 minutes to get the part. Instead, maintenance simply deferred the trim switch and placarded it INOP. The captain spoke to maintenance regarding the deferral and was told to use the backup trim switch in lieu of the failed captain’s yoke trim switch. The FO flew the next leg from LGA to ATL and no incidents were reported. No further maintenance was done on the captain’s trim switch in ATL.
On leg from ATL back to LGA the taxi out and the takeoff were normal. The captain was the pilot flying. During takeoff, the airplane climbed at about 4000 feet per minute, and the captain said this seemed normal since they were light with only six passengers. While the FO waited the switch to departure, the captain said to declare an emergency for runaway trim. The FO saw the captain struggling to control the airplane. It took both pilots pushing forward on the control column to keep the airplane from pitching up.
They reported to ATC that they were in a stalling situation. The FO pressed the button to disengage pitch trim system 1, the system identified in the message. Airspeed dropped to at least 138 knots before they regained control of the airplane. When asked about performing the initial action items to stop the runaway pitch trim, the captain said he “kept pushing the button” but had to keep both hands on the yoke to control the airplane. The captain had the quick reference card in his lap but could not pick it up and read it as all his efforts were spent keeping both hands pushing on the yoke. The FO stated that once he started flying the airplane at about 10,000 feet, with System 1 disengaged, he was able to trim the airplane nose down and regain some airspeed. They returned to ATL and landed uneventfully.
What caused the trim runaway? Post-incident examination of the captain’s pitch trim control switch identified imprint marks on the back of the switch, indicating that, at some point, the switch was installed upside down—probably during maintenance after the first leg when the pitch trim switch was partially removed and then reinstalled and deferred and not functionally tested. The NTSB felt the captain subconsciously used the manual trim switch even though it was placarded INOP.
Epilogue
The British Air Accidents Investigation Branch (AAIB) investigated a 6 September 2017 fatal crash of a Piper Navajo (PA 31) that they suspected was a trim runaway. They found the elevator trim tab close to the nose down limit but did not determine the cause. Interestingly, the report references an FAA research paper saying: “The FAA research paper indicated that general aviation pilots are often not fully aware of the systems onboard the aircraft they fly, and that they may not experience autopilot failures prior to their first need to respond to one as pilot in command.” [Emphasis added.] The AAIB went on to say the FAA studies, previous events and the findings from this investigation have shown that, due to possible high control forces, trim runaway can be a difficult condition from which to recover.
Pilots flying with manual electric trim, auto trim or artificial feel systems that utilize the trim servos need to understand how to recognize a trim runaway and the immediate action needed to disable the trim. Further, with an instructor aboard and at a safe altitude, a trim runaway should be simulated to drive home how difficult aircraft control will become.
Bob Teter is a retired CFI and avionics engineer. He flew several different aircraft with manual electric trim but never received instruction on handling a trim runaway. Don’t let that happen to you.