With “steam gauge” round dials, the airspeed reading was mechanically determined inside the airspeed indicator. Likewise, the altimeter had its own independent mechanical movement, and the vertical speed indicator had a similar arrangement.
In today’s digitally integrated cockpits, the altitude, airspeed, and vertical speed are developed from solid state sensors inside an air data computer (ADC) or air data module (ADU). This article will discuss how the air data information is generated in today’s “glass cockpit” and what to expect if the pitot tube or static port is obstructed.
Airspeed
An airspeed indicator is typically the only instrument in the airplane requiring both pitot and static connections and an electronic instrument is the same. The difference between the pitot pressure and ambient (static) pressure directly relates to the speed of the aircraft through the air.
The pitot tube is plumbed to a differential pressure sensor inside the ADC. On one side is the air pressure from the airstream at the front of the pitot tube, and on the other side of the sensor is the static air pressure plumbed from the static port(s).
The sensor uses a piezoresistive silicon sensing element. The resistance of the element changes as the pressure difference between the pitot and static changes. This differential pressure, called dynamic pressure, is converted by a microcontroller into indicated/calibrated airspeed. The piezoresistive element is also sensitive to temperature changes, so the airspeed calculation needs to compensate for the element’s temperature. Other than that, the measure of airspeed is straightforward and does not need an expensive specialized component.
Altitude
Altitude is measured solely from a static port(s) pressure measurement, but the static pressure measurement needs to be more precise for altitude than airspeed. The sensor used for this measurement is still a differential pressure sensor, but the “other side” is a vacuum, established during manufacture.
Before the design and manufacturing processes improved to allow a piezoresistive sensor to be accurate enough for this measurement, vibrating cylinders (United Aircraft) or vibrating diaphragms (Sperry) were used. For the vibrating pressure sensors, the change in static pressure would cause the vibration frequency to change. The frequency change was then converted to altitude.
Implementation of Reduced Vertical Separation Minimum (RVSM) required even more accurate static pressure measurements. Improvements in the manufacturing processes, such as “suspending” the piezoresistive silicon sensing element in a stress-free mount, helped improve the reliability and accuracy of the silicon sensors. Today silicon sensors can be universally used, including in RVSM-certified systems.
All Plugged Up
On pitot lines, the most common cause of plugging or blockage is trapped water, ice, or insects. The pitot tubes have a drain hole for water, but these can be overwhelmed during a pressure washing or a flight in heavy rain. Additionally, water vapor (think hot, humid air) can enter the probe and condense past the pitot drain hole. The water can cause errors in airspeed (due to constriction of the line) or total blockage.
Water trapped in the line is also a concern if it freezes. Heaters are incorporated into the pitot tubes to keep the tube ice-free. Air-transport aircraft had water traps in the pitot line (like a Mason jar) that would catch and retain the water. The water would be dumped at the next maintenance interval. Some General Aviation aircraft have a “tee connection” installed at the lowest point in the line. This can then be opened to drain any existing water and then resealed. In specific Piper models, there was a pneumatic drain for clearing the line.
For the static ports, the usual reason for a clogged line is tape not being removed after washing, painting, polishing, or maintenance activities. Water can enter the static lines, although it is not as common as with the pitot line(s). Light aircraft do not normally have static port heaters unless certified for flight in icing condition. Many light aircraft have provisions for draining water from the static line, similar to what is done on the pitot line.
Since a plugged line happens infrequently, there will be a natural startle factor. The startle factor is especially true on takeoff. The pilot flying should habitually check, then say out loud, “airspeed alive,” during the takeoff roll. However, even though the airspeed has become “alive,” it doesn’t mean everything is fine.
If the pitot line is blocked during the takeoff roll and you haven’t noticed the zero airspeed before you rotate, after rotating you’ll see a low airspeed that’s increasing.
In this case, the pressure sensor sees a constant pressure (field elevation) on the pitot side and a decreasing static pressure as the aircraft climbs. Therefore, the sensed dynamic pressure and the displayed airspeed will increase as the aircraft climbs. Since the differential pressure is higher than usual, the airspeed will continue to increase as you climb and accelerate past the actual airspeed moving toward the high-speed limit.
However, if the blockage is in the pitot tube itself, before the small drain hole(s), the airspeed will stay near zero. (The drain hole provides near static pressure to the pitot side of the pressure sensor.) With a blockage limited to the pitot line, the altimeter and VSI will operate normally.
If the static ports are blocked, the airspeed will initially be OK, but the static pressure will not decrease with altitude as it should. Since the air is trapped, the pressure in the static port lines will still indicate the air pressure at the airport. The airspeed will increase during the takeoff roll, as it normally does, but the airspeed will decrease quickly when you start your climb.
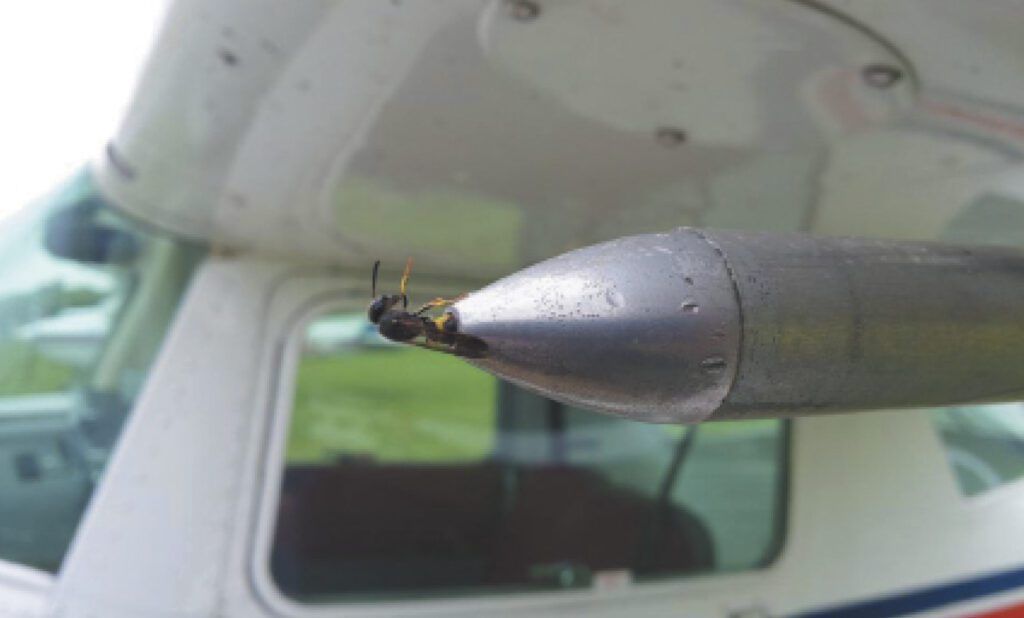
Why? Assuming you are climbing at a fixed airspeed, the differential pressure between the incoming air (total pressure) and “stuck” static pressure will quickly decrease during the climb. Besides “Airspeed Alive,” “Positive Rate” should also be a standard call out. With a plugged static source, you should have noticed the altimeter and VSI haven’t budged, but if you concentrate on the airspeed decay and push the nose over to maintain what you think is the proper airspeed, it could be a fatal mistake.
The good thing with a plugged static line is that you can switch to the alternate static source. In an unpressurized aircraft, this will open the static line to allow cabin pressure to substitute for the outside static pressure. There will be some error in the altitude due to the difference between the inside cabin pressure and the outside pressure, but it should be manageable.
Digital Cockpits
In the “old days,” a blocked pitot tube was less severe than a blocked static line because the former only affected the airspeed indicator. However, today with integrated avionics a blocked pitot tube can affect more than just the displayed airspeed. Several avionics manufacturers have integrated envelope protection into their systems. If the system detects an airspeed that requires stiffening the pitch-feel or pushing the nose down to prevent stalling or pitching up to prevent overspeed the system will do that.
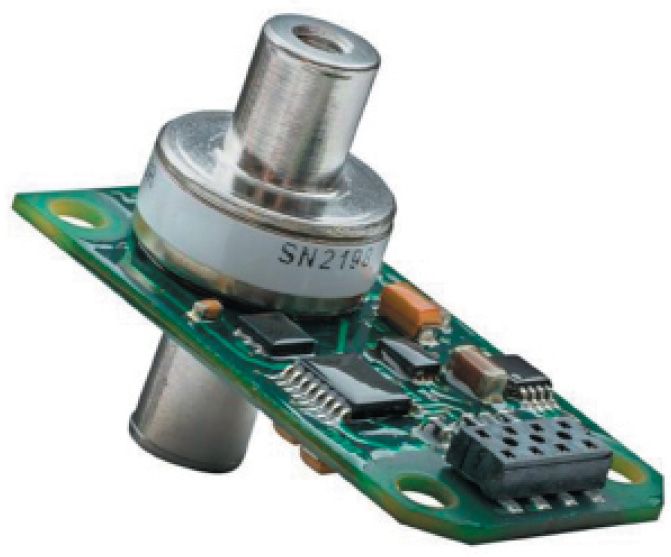
It’s fine usually, but it isn’t when you have an air data “plumbing” issue. Worse than that, it has come to my attention (see “ICE IS NOT NICE’ by Fred Simonds in January 2022) that illogical failures of the PFD have also been reported with pitot/static failures. Quoting from the article: ”It’s scary that a pitot/static failure triggered unrelated illogical alarms. This inexplicable malfunction has been reported in Aspen, Avidyne, and Garmin G500 primary flight displays.”
Frank Bowlin’s sidebar “Illogical Failures” in the same article provides more information on what is causing this. (Hint: Using air data measurements to aid the micro-electro-mechanical-system (MEMS) calculations. The MEMS sensor set is not accurate enough to calculate attitude and heading without other added (aiding) information.) [Aspen and Garmin have since released fixes to correct this situation. It is unknown if Avidyne released a fix.] See the sidebar “Why Did It Do That?”
Simulators
There are a few interactive pitot/static system simulators available online. These allow you to block the pitot, static, and drain holes alternately and then climb or descend. It’s a lot safer than experimenting on your aircraft. It also allows the selection of the alternate static source. One such simulator can be found at http://luizmonteiro.com/Learning_pitot_Sim.aspx. When you use the simulator, run the cursor along the baseline to simulate gaining airspeed during the takeoff roll before climbing.
What Do I Do Now?
If you have a failure, there’s a lot to think about. Determining what information is correct and what is erroneous will require good system knowledge. Don’t jump to conclusions. What other information can you use to determine what’s false and what’s true? Having an angle of attack Indicator can save the day. (However, it needs to sense the actual airflow, not some of the newer units using derived data.)
You should always check the pitch and power against what is shown on the air data instruments. You need to know the normal pitch and power settings for a climb, cruise, and approach. Use those as your go-to setting while sorting through the issue. Don’t get wild with pitch or power changes beyond what is normal for that phase of the flight unless of course you have already entered an unusual attitude.
Wind noise can also provide clues on airspeed conditions. Are the flaps rumbling more than usual, indicating a higher-than-normal airspeed? If you have visual conditions, the gold standard is to check the horizon on the windscreen and set your power accordingly. You need to sort it out quickly in instrument conditions, but do not get fixated on only one instrument. Cross-check everything, and while time is critical, as I said, don’t jump to conclusions.
Help from ATC
ATC cannot help you with your altitude. The source of the altitude for the transponder (what ATC sees) is usually from the same static port as your altimeter. It doesn’t matter if the transponder gets its pressure altitude from an “altitude encoder” or an air data computer/module it is from the same static source.
The controller can help by giving you your ground speed, but if you have a plugged static source, the altitude they show will match what you see in the cockpit. No help there. Switch to your alternate static source. Of course, ATC can help vector you to VMC.
Having erroneous airspeed and altitude and possibly losing the attitude information on the primary flight display is a serious situation. If in VMC, stay there; do not enter IMC. If already in IMC, work with ATC to get to visual meteorological conditions. You might think I’m fine; I can fly using the standby instruments, but an upset or turbulence can make things very demanding, and having a good visual reference helps immensely.
Bob Teter is a retired CFI, Commercial SEL, MEL pilot who had a 43-year career in the design, development, and flight testing of avionics systems.